(If you would rather listen than read, just click play above.)
Hello, everyone, and welcome back to Battery Week!
We’ve talked about why lithium-ion batteries (LIBs) are so important and we went through a basic primer on how they work. Today, we’re going to get into the competition within the broad lithium battery family, among all the different kinds of batteries that use lithium and exchange charged lithium ions. (See the previous post for a full list.)
There are a few clear leaders — lithium nickel manganese cobalt oxide (NMC), lithium nickel cobalt aluminum (NCA), and lithium ferro phosphate (LFP) — that have achieved mass market scale and several others looking to get in on the action.
The market prize is likely to exceed a trillion dollars within the next decade, so if any of these competitors can even carve out a substantial niche, it could be worth billions. Let’s look at the players.
Better NMC and NCA
The bulk of LIB research these days is going to improve the dominant batteries on the market, mainly by reducing the amount of cobalt (the most toxic and expensive ingredient).
Most EV makers use NMC batteries; Tesla uses NCA. In the past, it’s been difficult to push down the amount of cobalt in these batteries (it plays an important balancing role), but manufacturer LG recently introduced an NMC 811 battery: 80 percent nickel, 10 percent manganese, 10 percent cobalt. GM will use them in its new line, including in the Hummer, and Tesla will put them in some of its Model 3s in China.
Most big battery manufacturers, including Panasonic (which supplies many of Tesla's batteries), have vowed to gradually reduce and eventually eliminate cobalt.
Nickel is the key to energy density. Tesla, VW, and others are working on special high-nickel battery varieties that will be used for specialty vehicles that require extra-high energy density, like larger SUVs and trucks.
But not every vehicle needs that, and nickel supply constraints are looming, so work is also being done to further boost manganese — a much more stable, abundant material — and reduce cobalt.
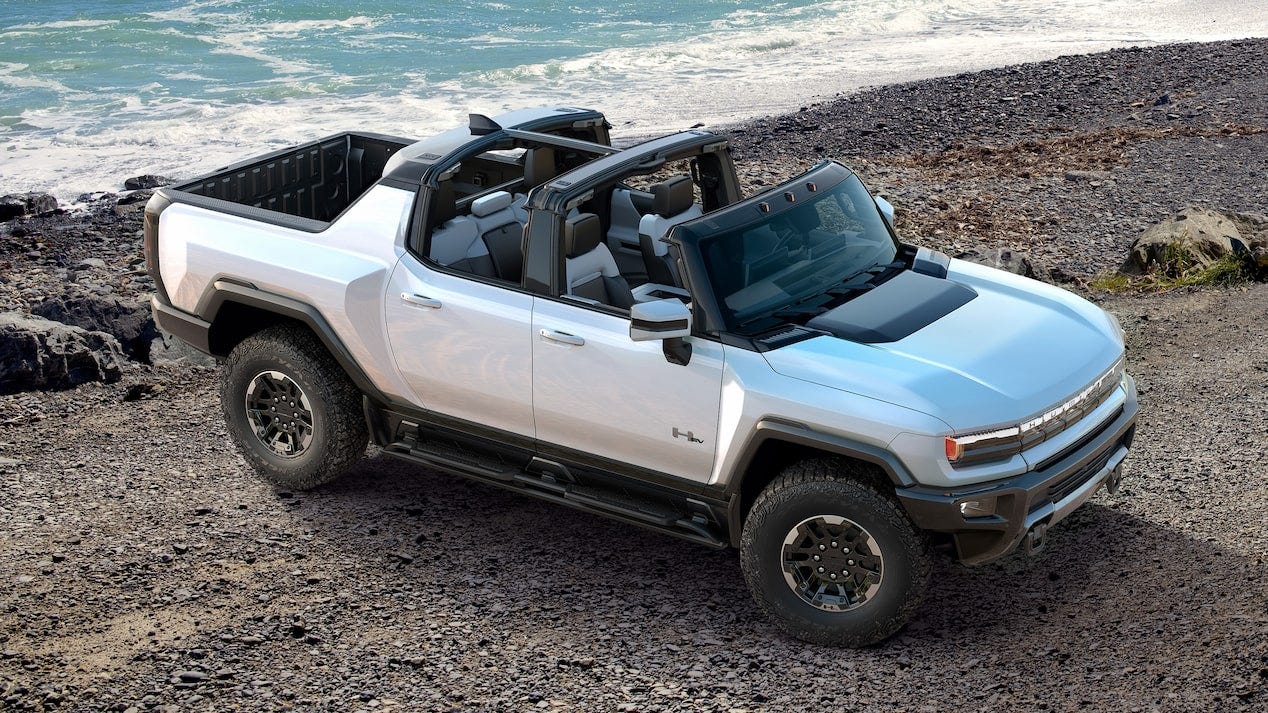
Silicon anodes
Many LIB developers are experimenting with silicon as an anode coating, partially or completely replacing graphite. Tesla has been working to increase the proportion of silicon in its anode since at least 2015.
Silicon holds on to nine times more lithium ions than graphite, so energy density improves (range expands by 20 percent), and a silicon battery can charge and discharge much more quickly than graphite batteries, so power density improves as well. But silicon expands when it absorbs ions, so it breaks down quickly; cycle life is still much lower than graphite. If engineers can overcome that problem (and Tesla has vowed it can), LIBs could take a leap forward soon.
SILA Nanotechnologies, in its brief on the future of LIBs, considers silicon anodes the biggest potential near-term market-shifting breakthrough in the space. It summarizes:
[T]here are no high-volume commercial Li-ion batteries (yet!) in which a silicon anode entirely replaces the graphite one. When it does arrive, the reward will have been worth the wait. We expect automotive cells with NCA or NCM cathodes paired with Si-dominant anodes will increase energy density by up to 50%, thereby dropping the $/kWh cost by 30-40% in less than a decade.
That is a mind-boggling prize, if any manufacturer can unlock it. (Read Canary’s Julian Spector on Sionic, a battery company that has recently debuted a silicon anode that it says can fit into existing LIB manufacturing.)
Silicon anodes are technically “cathode agnostic,” though most testing so far has used NMC cathodes. If engineers can crack the code and make silicon anodes with high cycle life, it could benefit any and all cathodes (e.g., see LFP below).
Fluorides as cathodes
One thing I didn’t mention about silicon-as-anode: it doesn’t operate via intercalation. Instead of nestling into the anode, ions react with the silicon and bond with it, a process called “conversion.” That makes it more difficult to peel the ions off without damage, but it can hold way more ions.
With anodes (which are the limiting factor on most batteries now) improving, there’s more room for cathode improvement. SILA is big on research into fluorides — it cites metal fluoride-based cathodes (like iron fluoride or copper fluoride) and sulfur-based cathodes — which also operate via conversion rather than intercalation and can also store more ions. It writes:
It’s plausible that with a conversion cathode and an engineered low-swell silicon anode, the cycle life of Li-ion can be extended all the way to 10,000 full cycles while also having the highest energy density in the market — thus breaking the [power vs. energy] compromise.
SILA believes it’s only that combination — a conversion-based anode and a conversion-based cathode — that can bring LIB prices down to “~$50/kWh by 2030 and ~$30/kWh by 2040.” If it happened, that would be absolutely wild and almost certainly crush all competitors.
Lithium ferro phosphate (LFP)
LFPs, which use a lithium-iron compound as cathode, were among the first LIBs to commercialize. They are already standard in China, used in its ubiquitous scooters and small EVs. “The big Chinese battery makers — BYD and CATL and Lishen — each one of those is larger by itself than any other battery company that's not in China,” says Lou Schick, director of investments at Clean Energy Ventures, “and they have been making lithium iron phosphate cells for 10 years.”
A few years ago, it looked like LFPs were going to be displaced by NMCs and NCAs, but lately they’ve made a comeback and now have a decent case that they could take the lead in the EV and stationary storage markets. They have already captured almost half of the Chinese EV market.
LFPs use lithium ferrophosphate (LiFePO4) as the cathode, replacing nickel, manganese, and/or aluminum. The advantages relative to nickel-based competitors:
cheaper on a materials basis (though not yet on $/kWh);
higher cycle life (Matt Roberts, previously executive director of the Energy Storage Association, now working at battery company Simpliphi, says his company’s LFP batteries are warrantied for 10,000 cycles, compared to 2,500 to 5,000 for cobalt batteries.);
higher power density;
high safety and low toxicity (“They're almost literally bulletproof, in that they can't catch fire,” says Schick.);
replaces problematic and/or rare metals with iron, which is safe and abundant.
In exchange for these advantages, LFPs offer lower energy density (there are fewer spaces for ions to intercalate). However, because they are so safe, LFPs do not require the same protective packaging as NMCs and NCAs, so they can gain some of that efficiency back at the pack level. Tesla says that, while LFPs have 50 percent of the energy density of their high-nickel competitors, an LFP-based vehicle can still get 75 percent of the range.
VW announced last month that, starting in 2023, it would be “employing lithium iron phosphate, or LFP, in entry models; nickel-manganese in volume models; and nickel-rich NCM in high-end models.”
Tesla said more or less the same thing at its Battery Day event in 2020. It plans to use LFPs for an upcoming cheap (under $25,000) vehicle, the Model 3, and commercial energy storage.
Current LFPs are not going to feature in high-performance vehicles, but most vehicles aren’t that. They are “good enough, essentially, for any kind of commuter car,” Schick says. “I think you're going to see a whole bunch of economy cars that are LFP.” LFP will be used in taxis, ride-share vehicles, and fleet vehicles, along with scooters and rickshaws and motorcycles. It will be the cheap, reliable, everyday option.
And if LFPs can make use of silicon anodes, they could potentially nudge up into the over-300-mile range category.
LFP in energy storage markets
Energy density is also less important in the energy-storage market, where price, capacity, and safety rule.
LFP’s high cycle life and low costs make them attractive in the grid-storage market. As Julian Spector wrote in February at GTM:
In 2015, LFP batteries only served 10 percent of the grid storage market, according to research from Wood Mackenzie. NMC dominated, with more than 70 percent market share. But since then, NMC's market share has trended down while LFP's rose. Analysts predict LFP will become the leading chemistry for grid batteries by 2030, capturing 30 percent of an increasingly diversified market.
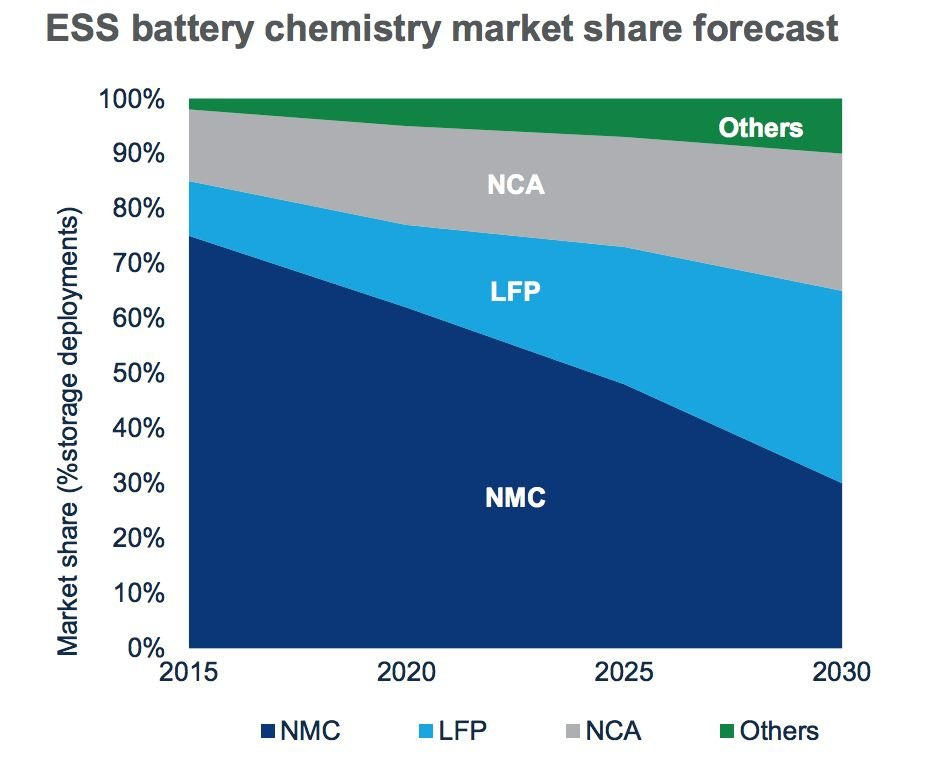
As for distributed, behind-the-meter storage, in some markets like California and New York City, Tesla home batteries (still NMC) are not allowed inside garages, thanks to the risk of thermal runaway, which can lead to fires. LFPs have passed an extensive regimen of safety tests and will be available everywhere; that gives them a tangible market advantage.
Roberts is convinced the safety issue is going to rise in salience, thanks to the repeated recalls from manufacturers like LG Chem. (The latest is going to cost Hyundai a cool $900 million.)
“What's your levelized cost of energy?” Roberts asks. “You're out there quoting, ‘I can do $100 a kilowatt-hour for a battery pack.’ If in two years, though, you have to do a billion-dollar recall, when does that get factored into the LCOE?”
With sufficient manufacturing scale, the price of any battery approaches the price of its materials, and LFP uses incredibly cheap materials. If it scales sufficiently, it could potentially get cheap enough to dominate the storage market, fighting off other LIBs in the home-storage market and other chemistries and form factors (which we’ll look at in the next post) in the bulk-storage market.
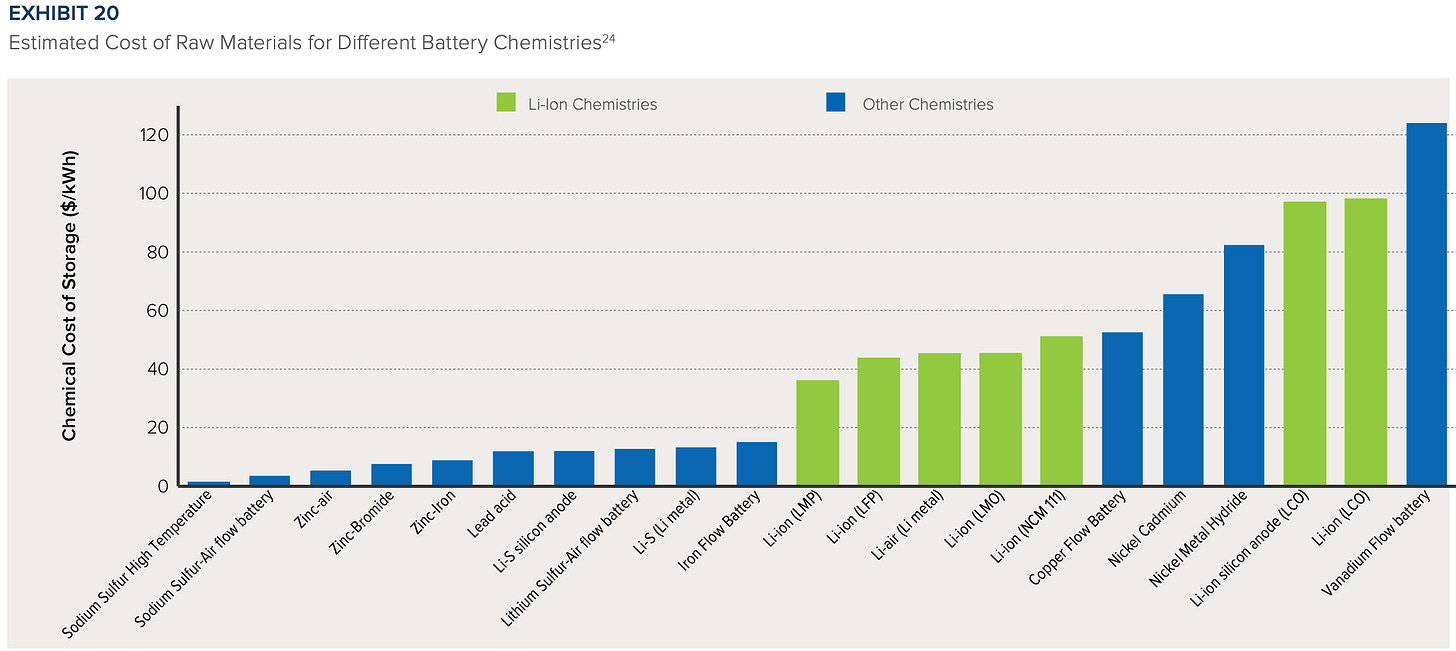
“Of all the lithium-ion chemistries, LFP may play the largest role in accelerating the world’s transition to sustainable energy,” says Jordan Giesige, who makes battery explanatory videos under the moniker The Limiting Factor. (They are superb; I cannot recommend them highly enough.)
Lithium manganese oxide (LMO) and lithium manganese nickel oxide (LMNO)
Manganese is abundant, safe, and stable at a wide variety of temperatures, though its energy density is lower than cobalt or nickel. Because LMOs don’t contain cobalt and avoid the threat of thermal runaway, they are used in medical equipment, as well as power tools, electric bikes, and EVs.
“The original Nissan LEAF was a lithium manganese oxide cathode,” says Dan Steingart, a materials scientist and co-director of Columbia University’s Electrochemical Energy Center, “and the Nissan LEAF has never had a battery that that initiated a fire.”
The LEAF also didn’t go very far on a charge, though — LMO may have trouble escaping its niche.
LMNO (“high-voltage spinel”) batteries try to retain some of the energy density of nickel while replacing cobalt. According to a 2020 study in the Journal of Power Sources, in the search for “novel cathode materials with high energy density, low cost, and improved safety,” LMNO is “one of the most promising candidates yet to be commercialized.”
LMNO batteries will need to boost their still-struggling cycle life before they can compete with more-established chemistries.
The next three batteries use lithium or lithium compounds as the anode rather than the cathode.
Lithium sulfur (Li-S)
Li-S burst on the scene to some excitement in the late ‘00s, demonstrating that a cell with lithium as the anode and sulfur as the cathode — two elements with extremely low atomic weight — could double the specific energy of conventional LIBs. Plus sulfur is incredibly cheap.
One problem is that sulfur has very low conductivity, so something (usually carbon) has to be added to pull in the ions. More importantly, Li-S batteries degrade quite quickly and have low cycle life. To date, they remain commercially unavailable. (This paper reviews the remaining challenges.)
Lithium metal anodes
Simple, solid lithium metal makes for a great anode, in that it is highly prone to releasing electrons and ions. Use of lithium metal as an anode actually dates back to the 1970s, preceding LIB development. In a lithium-metal battery, charged lithium ions “plate” on (attach themselves directly to) the metal anode.
The problem is that lithium is highly reactive and ions tend to form “dendrites,” or tree-like formations, that reduce energy density and cycle life and increase the chances of a short or fire. It was problems with lithium’s reactivity that originally led to the addition of graphite to the anode, so the ions could intercalate rather than plating. That was the birth of LIBs.
But researchers and developers have recently returned to lithium-metal, figuring out new ways to prevent dendrite formation. Losing the graphite on the anode drops weight and up to doubles energy density.
To date, lithium metal has typically been paired with a standard NMC cathode. US startup Lavle is building a gigafactory to produce just such batteries, expected to open in 2023. It is aiming first at markets where energy density is prized, like shipping and aviation.
Technically, though, lithium-metal is cathode agnostic. It could potentially work to enable rechargeability and better performance from cheaper cathode materials like zinc, aluminum, and sulfur. Based on pure materials costs, “the true least-cost system for a lithium-based, rechargeable battery is lithium metal and a sulfur cathode,” says Purdue University’s Rebecca Ciez.
Much of the R&D action, though, is around electrolytes. Lithium-metal batteries with liquid electrolytes are around (and still being researched), but it’s the solid electrolytes generating the most excitement.
Solid electrolytes (solid-state)
The liquid electrolytes used in most LIBs limit the kinds of electrodes that can be used and the shape of the battery cell; plus, they are often flammable, a safety hazard. Tons of research is underway on solid electrolytes that enable much higher energy density and can’t catch fire.
Many researchers expect solid-state batteries to set off a whole new round of innovation. RMI writes, “several solid-state companies are targeting 2024–2025 for initial EV commercial lines, but demonstrations would likely happen before then.” Companies with lithium-metal, solid-state batteries — like Solid Power and QuantumScape — have received huge investments from automakers and investors like Bill Gates.
Nonetheless, for all the hype, there is a considerable strain of skepticism about solid-state. The EV company Fisker, after years of big promises, abandoned solid-state entirely earlier this year. “It’s the kind of technology where, when you feel like you’re 90 percent there, you’re almost there,” founder Henrik Fisker told the Verge, “until you realize the last 10 percent is much more difficult than the first 90.”
“The cost and safety of current lithium-ion tech is improving so rapidly that a technology that's 10 years away, in [Fisker’s] estimation, is just not worthy of pursuit,” says Roberts. “At the end of the day, energy density is just not critical in a lot of applications.”
Schick is blunt: “None of the solid-state lithium batteries are on track to do anything that anybody cares about.”
“While there are technical reasons why this technology appears to be the holy grail of batteries,” writes SILA Nanotechnologies, “the reality is that even if the technology works (and that is a big ‘if’ after 40 years of development) it is unlikely to find more than niche opportunities in the market.” (Read Jason Deign on the current solid-state market.)
Let’s call this one an important Maybe.
Lithium titanium oxide (LTO)
LTO batteries have lithium-titanate nanocrystals coating the anode, which increases surface area and allows for many more electrons to be released much faster than graphite. Consequently, they have incredibly high power density (they can release energy quickly) and can recharge faster than any other LIB. They also have high cycle life and high recharging efficiency.
They are lower voltage than conventional LIBs and thus have lower energy density, but because of this they are also extremely safe to operate.
“The performance characteristics are amazing,” says Roberts, “but it's just crazy expensive.”
For now, LTOs are used in some EVs and smaller applications like e-bikes. If they come down in price, they could find other niches where power density is important, like industrial machinery.
Lithium-air (Li-air)
Out toward the research frontier is Li-air, which uses lithium metal as the anode, a variety of materials as the electrolyte (that’s where research is most intensive), and as the cathode … air. Yes, air. Lithium exchanges electrons and ions with the air, through the electrolyte. Wacky.
Because it jettisons the entire weight of the cathode — air is quite light — Li-air has incredibly high specific energy (energy per unit of weight), theoretically as high as the specific energy of gasoline. In practice, only a fraction of that potential has been demonstrated, but even that fraction is about five times the specific energy of conventional LIBs.
All sorts of improvements in electrolytes, cycle life, and scalability will be needed before Li-air will become practical, but in terms of 2030 dark horses, this is one to watch.
So that’s a review of the lithium-based battery chemistries jockeying for position in a trillion-plus-dollar market.
In my next post, I’ll look at a few non-lithium-based chemistries that are hoping to capture some of these niches — zinc and flow and liquid metal, oh my.
Share this post