(If you don’t want to read, you can listen. Just click play above.)
Greetings! Welcome back to Battery Week here at Volts. In my last post, I went over why lithium-ion batteries (LIBs) are so important to decarbonizing both transportation and the electricity sector.
Next week, we’re going to get into the nuts and bolts of different kinds of LIBs, to see how different chemistries offer different kinds of performance and are competing for different market niches.
Before that, though, it’s worth the time to do a little review of battery basics. If you’re like me-a-month-ago, you probably have a hazy understanding at best of the structure of batteries and the processes involved in running them.
I’m not going to get into any complicated chemistry — believe me, no one wants that — but I thought it would be helpful later, when we get into the competition within battery markets, to have some rudimentary terms and concepts clear in our heads.
Batteries 101
F’ing batteries, how do they work?
As the name suggests, electrochemical batteries store energy via chemical reaction. Discharging the battery involves a chemical reaction that produces electrons; recharging the battery involves a chemical reaction that stores electrons.
The basic unit of the electrochemical battery is the cell. In the cell, two electrodes — negative (anode) and positive (cathode) — are separated by an electrolyte.
When the anode and cathode are connected in a circuit, two things happen.
1. Negatively charged electrons flow from the former to the latter, generating power. The amount of power is determined by two factors:
current, the number of electrons traveling in a given circuit, and
voltage, the force with which the electrons are traveling.
Power = current X voltage. It’s like a river: the force exerted by the water will depend on how much there is and how fast it’s moving. You can get the same force with less water if it moves faster, or with slower water if there’s more of it. Similarly, you can get the same power with less current if you have more voltage, and vice versa.
2. The anode releases positively charged ions into the electrolyte, to balance the reaction, and the cathode absorbs a commensurate amount. (Some batteries have a thin semi-permeable barrier within the electrolyte to regulate the flow of ions.)
Recharging a battery basically involves reversing the reaction, returning the electrons and the ions to the anode.
The anode will be a material that gives up electrons easily in chemical reaction with the electrolyte. The cathode will be a material eager to absorb them. The propensity to shed/absorb electrons is known as standard potential, and the difference in standard potential between the anode and cathode will determine the battery’s total electrical potential. The bigger the difference, the more potential.
The whole game of battery design and development is to find a combination of anode, cathode, and electrolyte that performs well along a broad set of criteria — holds a lot of energy, releases energy quickly, operates safely, lasts a long time, is cheap, etc.
The tragedy of battery development is that there are always trade-offs. High performance on one criterion generally means lower performance on another. Optimize for holding more energy and you limit how quickly energy can be released; optimize for safety and you limit energy density; and so on.
Battery development has seen dozens of chemistries come and go, but four have stuck and scaled to mass-market size: lead acid, nickel cadmium (Ni-Cd), nickel metal hydride (NiMH), and lithium-ion (Li-ion).
LIBs have hit on a combination of anode, cathode, and electrolyte that performs well enough along several criteria (especially cost) to work for most short-duration applications today. They dominate consumer electronics, electric passenger vehicles, and short-duration grid-scale storage, and are expanding in other markets as well (though lead-acid batteries remain a $45 billion global market). They have gotten very cheap and a large-scale manufacturing capacity has grown up around them.
Let’s take a closer look at LIBs.
Lithium-ion batteries 101
LIBs have been around in commercial form since the early 1990s, though obviously they’ve improved quite a bit since then.
Today’s most common and popular LIBs use graphite (carbon) as the anode, a lithium compound as the cathode, and some organic goo as an electrolyte. They boast two key advantages over prior battery chemistries.
First, they need very little electrolyte. LIBs are what’s known as “intercalation” batteries, which means the same lithium ions nestled (intercalated) in the structure of the anode transfer to be intercalated in the cathode during discharge. The electrolyte only has to serve as a conduit; it doesn’t have to store many ions. Consequently, the cell doesn’t need much of it. Saving on electrolyte saves space and weight. (Bonus: the process is almost perfectly reversible, which gives LIBs their high cycle life.)
Second, LIBs squeeze lots of energy into a small space. Lithium is the lightest metal (at the upper left corner of the periodic table) and extremely energy-dense, so LIB cells can work with electrodes 0.1 millimeters thick. (Compare lead-acid electrodes, which are several millimeters thick.) This also makes LIBs smaller and lighter.
Because they are lightweight and high energy density, LIBs got their initial foothold in small electronic devices, phones and laptops and the like. They scaled up quickly to run handheld power tools and lawnmowers and then completely took over electric vehicles. Recently they’ve scaled up further to create home storage batteries and giant stationary battery arrays for grid storage.
It’s worth noting that even the biggest LIB installation is just stacks upon stacks of cells, like Legos. LIBs are extremely modular — they can be scaled precisely to need.
LIB manufacturing
There are a number of ways of manufacturing LIB cells — button cells, pouch cells, prismatic cells — but the most common for portable and EV applications is the cylindrical cell. Think of it like a jelly roll. A super-thin metal anode is coated with a film (usually graphite). Then a super-thin separator is laid on top. Then a super-thin metal cathode coated with a film (usually some lithium compound) is laid on top of that. Several layers are stacked this way, and then the whole thing is rolled up and packed into a cylinder. Before the cylinder is capped, electrolyte goop is injected to infuse between the layers.
Cells are then clustered together into modules, which are in turn clustered together into packs.
There’s a whole active area of LIB innovation around cell design. Tesla recently debuted a new, bigger cylindrical cell, the 4680 (46 millimeters wide, 80 mm tall), with improved … everything — energy, range, and power.
Tesla is also putting these cells together into packs that form part of the structure of their vehicles, which will reduce overall weight and complexity.
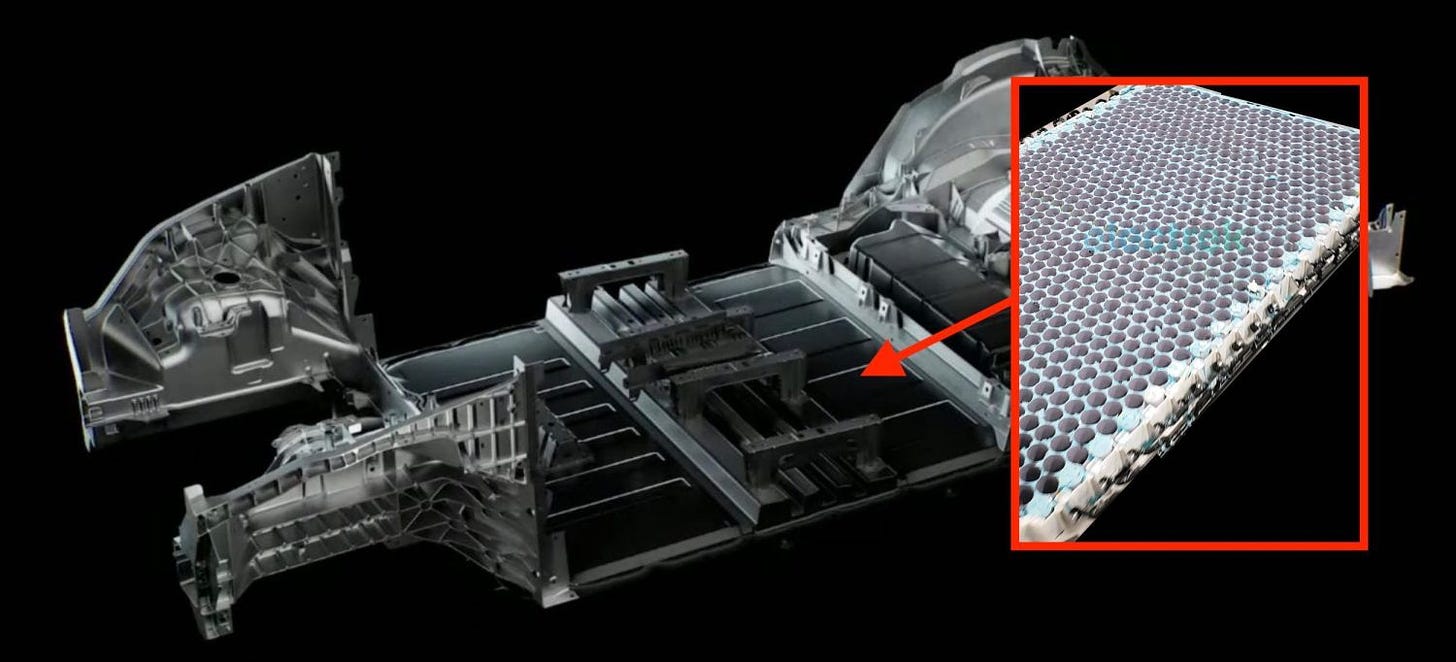
I’m not going to get into LIB manufacturing innovation too much, other than to note there’s a lot going on there.
The manufacturing techniques that produce LIBs are being continuously refined, a process that is accelerated by scale. According to RMI, “lithium-ion battery suppliers are poised to reach at least 1,330 GWh of combined annual manufacturing capacity by 2023.” According to S&P Global, “global LIB capacity is set to increase 218% between 2020 and 2025.” That’s a lot of scale.
The main thing to take from the boom in LIB manufacturing is that any competitor to LIBs will need to take advantage of existing manufacturing processes. “The way these battery factories are building up now,” says Dan Steingart, a materials scientist and co-director of Columbia University’s Electrochemical Energy Center, “they’re so capital-intensive that whatever chemistries come next will be produced and manufactured in such a way that they leverage existing infrastructure if at all possible.”
This will be important later; some LIB competitors can slipstream into existing manufacturing and some can’t.
For Battery Week, I’m going to focus less on manufacturing (and disposal) and more on the battery chemistries themselves — which ones are dominating and which have a chance of catching on.
Li-ion is a family of battery chemistries
LIBs are not a singular thing, but a family. They have in common that they use lithium in either the cathode or anode and exchange charged lithium ions.
This leaves quite a bit of room for different chemistries. There are many types of lithium compounds, many choices of anode or cathode materials to pair with them, and many choices of electrolytes.
That yields a very large matrix of possible combinations and chemistries, each with its different performance characteristics (and, sigh, acronym). We’re not going to cover all of them, though — even I have my limits. We’ll just hit some of the most-discussed alternatives.
The most common LIB chemistries used today are lithium nickel manganese cobalt oxide (NMC) and lithium nickel cobalt aluminum (NCA), which use compounds of those metals as the cathode. Lithium and nickel turn out to be a knockout combo — incredibly light and energy-dense. Nonetheless, there are others.
Here’s a list of the LIB chemistries we will at least touch on starting in my next post:
lithium nickel manganese cobalt oxide (NMC cathode)
lithium nickel cobalt aluminum (NCA cathode)
lithium ferro phosphate (LFP cathode)
lithium manganese oxide (LMO cathode) and lithium manganese nickel oxide (LMNO cathode)
lithium sulfur (Li-S, sulfur cathode)
lithium metal (anode) and solid state
lithium titanate (LTO anode)
lithium air (Li-air, lithium anode)
Why bother with any of these alternatives? Why not just stick to NMC and NCA?
There are two sources of pressure on the industry to diversify.
LIBs face pressure to diversify performance
The first is performance. Most LIB innovation to date has focused on energy density, for passenger EVs. In some applications, though, like home energy storage or fleet vehicles, energy density matters less than safety and cost. As use cases diversify, so do performance demands.
With that in mind, let’s take a quick look at the various metrics used to judge battery performance. RMI uses eight:
energy density (Wh/L): energy per unit of volume, or more prosaically, energy relative to space occupied, sometimes called “volumetric energy density”;
specific energy (Wh/kg): energy per unit of weight, sometimes called “gravimetric energy density”;
power cost ($/kW): cost per unit of power output (to return to our river analogy: cost per unit of force the river is capable of exerting at its peak);
energy cost ($/kWh): cost per unit of energy output (the amount of force exerted by the river over an hour);
cycle life: the number of times a battery can discharge and recharge before it falls below some threshold of capacity (usually set at 80 percent) due to degradation;
fast charge: how fast the battery can charge, i.e., how fast it can accept power;
safety: some batteries, particularly those with cobalt, suffer from “thermal runaway,” which means if one cell goes haywire and heats up, it heats up the next one, and so on in a self-reinforcing cycle that results in fires and battery recalls;
temperature range: the range of temperatures in which a battery can effectively operate.
As I said, it’s possible to optimize for one or a small set of these, but doing so inevitably involves trade-offs in others.
This graphic from RMI compares some LIB chemistries along all these axes. The dark green lines are current performance and the light green is highest theoretically achievable level:
As you can see, different chemistries excel on different metrics and will target different applications.
LIBs face pressure to diversify materials
Cobalt, used in standard NMC and NCA chemistries, is highly toxic, comes almost entirely from the Democratic Republic of the Congo, and is mined amidst terrible human rights abuses. Lithium and nickel are fairly nasty too, and may run into supply constraints as the market grows (nickel, in particular, is a source of current stress).
There’s lots of innovation underway to reduce the social and environmental impacts of materials mining, and increase supply, but, as we will see next week, there are also competing battery chemistries that eschew these problematic materials entirely.
Smart manufacturers like Tesla are diversifying their battery lines in anticipation of supply issues, trying to evolve away from cobalt and secure a steady domestic supply of lithium and nickel. (Biden’s infrastructure plan, which aims to kickstart a domestic EV supply chain, could help.)
Some battery diversity will happen, the question is how much
You can find people in the battery field who stress that conventional LIBs have too great a head start for anything else to catch up. In its white paper on the future of LIBs, SILA Nanotechnologies writes:
Technologies that claim they will replace Li-ion often grab headlines, but scale limitations make that impractical within a generation. It is for this reason that by 2050, while Li-ion will not constitute all of energy storage, it will be the most dominant chemistry by far, with most everything else relegated to niche applications.
Lou Schick, director of investments at Clean Energy Ventures, a venture capital firm that invests in clean technology projects, stressed to me the importance of scale and familiarity:
The only selection criteria for any project is, is it bankable? Can I get insurance for it? Is it consumer product? Any insurgent that wants to get to that state and is in a lab right now is 10 years away from being bankable, if they are very successful. So you're never catching up. And it has nothing to do with chemistry or physics.
You can find others who believe diversity is inevitable. “It's not like the Lord of the Rings, one ring to rule them all,” says Michael Burz, an engineer who founded and runs battery company EnZinc. “There will be different chemistries for different applications.”
Among the analysts more bullish on diversity are those at RMI, who wrote a report in 2019 called “Breakthrough Batteries” that surveyed possible competitors to conventional LIBs. They write:
Unlike the market development pathway for solar photovoltaic (PV) technology, battery R&D and manufacturing investment continue to pursue a wide range of chemistries, configurations, and battery types with performance attributes that are better suited to specific use cases.
RMI is convinced that other battery chemistries with other performance attributes will begin to find markets and scale up by the mid-2020s.
Chloe Holzinger, an energy storage analyst at the research firm IHS Markit, told me that diversity will be a market asset:
What we're going to see in the future is increasing diversity in all three of those areas [anode, cathode, and electrolyte]. Automakers will be able to take advantage of this diversity to make their portfolios robust against commodity price spikes and distinguish themselves from other automakers — “we're the only ones that provide this kind of battery.”
It’s possible that this disagreement amounts to less than it appears. Even skeptics agree that some competitors might find niches; the main disagreement seems to be over how fast that might happen and how big the niches will be.
After all, says Schick, in trillion-dollar markets, “if the market fragments by use case, the individual use cases can be quite enormous.”
Conventional LIBs have a huge head start, but the pressure to diversify may offer some hope to innovators both within the LIB family and outside it.
In my next post, I’ll get into some of that intra-family competition within LIBs, a space rife with ongoing innovation.
Mabel wishes everyone a Happy Spring.
Share this post